Fantastic Tips About Which Solder Is Better, 60/40 Or 63/37

Tin Soldering Lead Solder Stick 63 37 60 40 50 China
Solder Showdown
1. Understanding the Basics of Solder
Okay, let's get real about solder. It's that magical metal goo that joins electronic components together, creating circuits that power our gadgets. But not all solder is created equal. Two of the most common types you'll encounter are 60/40 and 63/37. The numbers refer to the percentage of tin (Sn) and lead (Pb) in the alloy. So, 60/40 solder is 60% tin and 40% lead, while 63/37 is 63% tin and 37% lead. Simple, right?
Now, you might be thinking, "Why should I care about these tiny percentages?" Well, those percentages affect how the solder melts, flows, and solidifies, which can significantly impact the quality of your soldering work. Choosing the right solder can be the difference between a solid, reliable connection and a cold, brittle joint that causes your project to fail. No pressure, though!
The world of soldering can seem a bit daunting at first, especially with all the technical jargon floating around. But trust me, with a little bit of knowledge and practice, you'll be wielding that soldering iron like a pro in no time. Think of this article as your friendly guide to navigating the solder selection process. We'll break down the key differences between 60/40 and 63/37, highlight their pros and cons, and help you determine which one is the best fit for your specific needs.
So, buckle up, grab your soldering iron (unplugged, of course!), and let's dive into the fascinating world of solder. We're about to uncover the secrets behind these two popular alloys and empower you to make informed decisions about your soldering projects. Get ready to level up your soldering game!
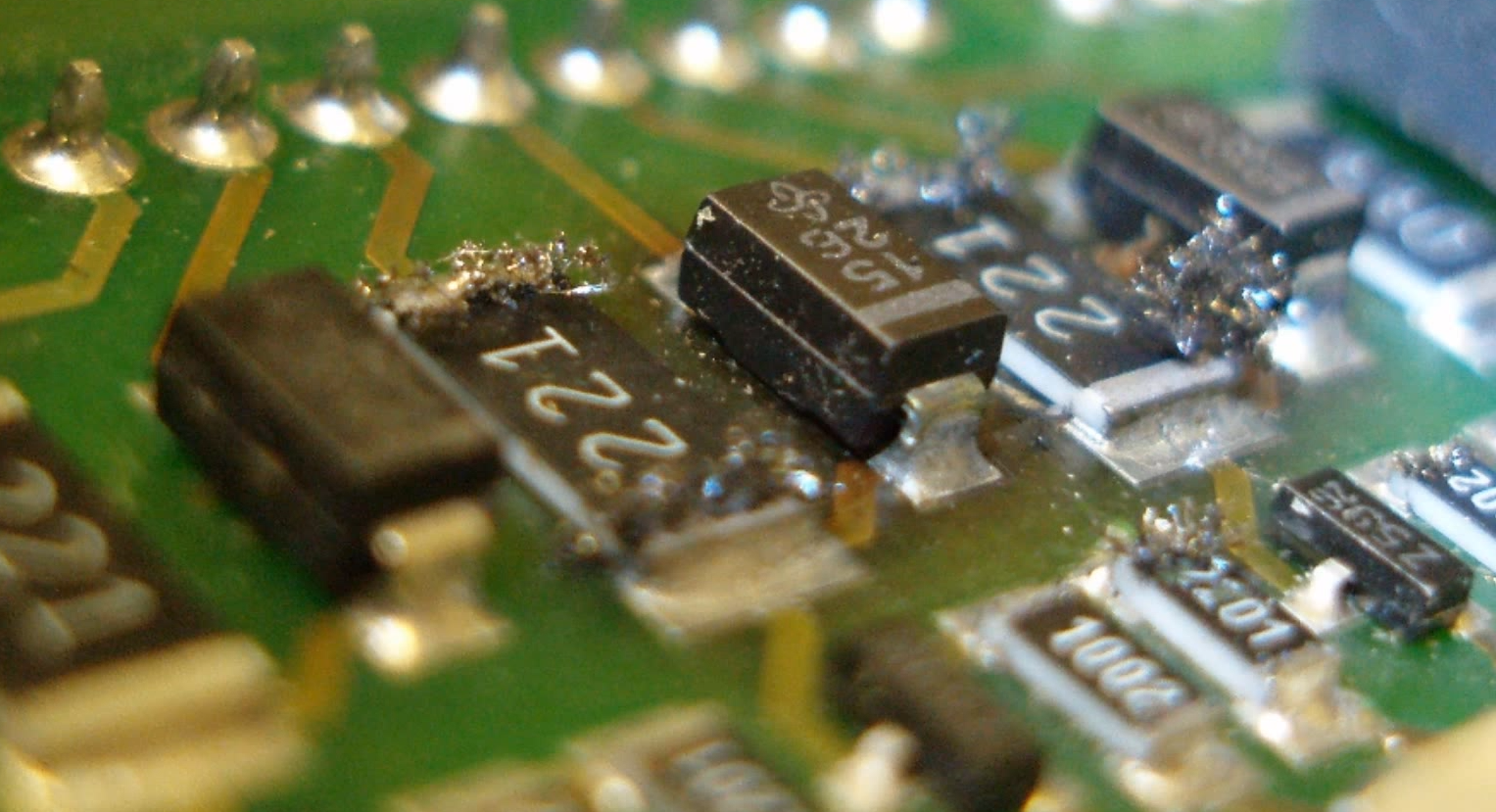
63/37 Vs. 60/40 Solder What’s The Difference? ElectronicsHacks
The Eutectic Advantage
2. The Magic of Eutectic Composition
Here's where things get a little sciency, but stick with me. 63/37 solder is known as a eutectic alloy. This means it has a single, distinct melting point (around 183C or 361F). When you heat it up, it transitions directly from solid to liquid, without a mushy, pasty phase in between. This sharp melting point is a huge advantage because it allows for more consistent and predictable soldering results.
Why is this important? Well, when solder melts and solidifies, it can sometimes create what's called a "cold solder joint." This happens when the solder is disturbed during the cooling process, resulting in a weak or unreliable connection. With 63/37 solder's sharp melting point, the risk of cold solder joints is significantly reduced because it solidifies quickly and evenly.
Think of it like making a cake. If your oven temperature fluctuates wildly, your cake might not bake properly. Similarly, with solder, a consistent melting point ensures a more stable and reliable connection. This is why many professionals and experienced hobbyists prefer 63/37 solder for critical applications where reliability is paramount.
Furthermore, the eutectic property of 63/37 solder makes it easier to work with, especially for beginners. The clean, crisp melting and solidification process allows for greater control and reduces the likelihood of errors. It's like having training wheels for your soldering iron! Okay, maybe not quite, but you get the idea. It makes the learning curve a little less steep.
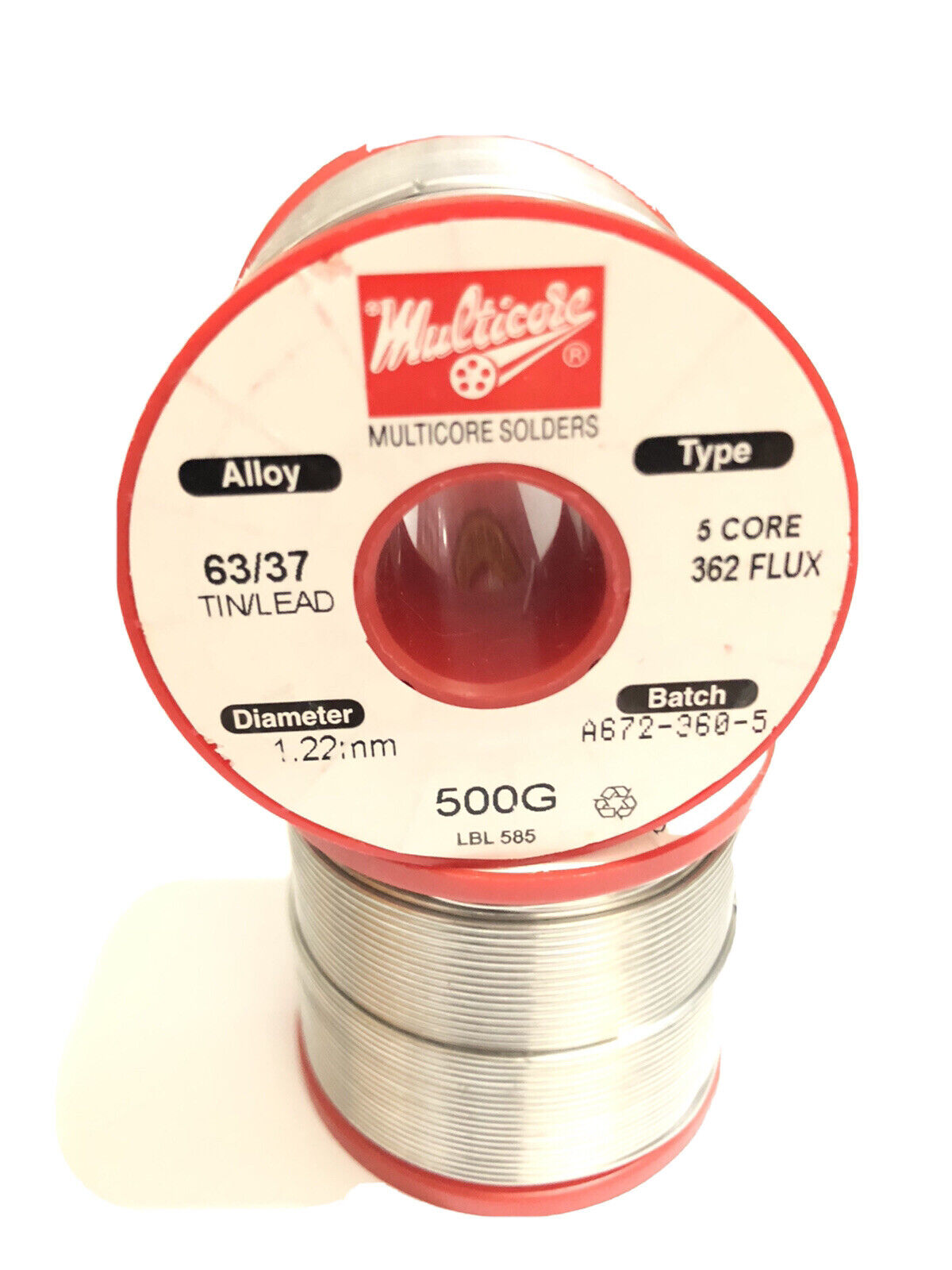
60/40 Solder
3. The Non-Eutectic Alternative
Now, let's not count out 60/40 solder just yet! While it's not a eutectic alloy, it still holds its own in many soldering applications. Unlike 63/37, 60/40 has a melting range, meaning it goes through a pasty phase as it heats up and cools down. This range is typically between 183C and 190C (361F and 374F). This broader melting range can be both a blessing and a curse.
One advantage of 60/40 solder is that it can be slightly more forgiving when soldering components with different thermal masses. The pasty phase allows you a bit more time to adjust the position of the components before the solder fully solidifies. This can be helpful when working with larger components that take longer to heat up.
However, the pasty phase also means that 60/40 solder is more susceptible to movement during the cooling process, which can increase the risk of cold solder joints. It's crucial to keep the joint perfectly still until the solder has completely solidified. This requires a steady hand and a bit of patience. Think of it like trying to balance a glass of water on your head — you need to stay perfectly still!
Despite the potential for cold solder joints, 60/40 solder is still a widely used and reliable option for many soldering tasks. It's often more readily available and slightly less expensive than 63/37, making it a popular choice for hobbyists and DIYers on a budget. Plus, with proper technique and a bit of practice, you can achieve excellent results with 60/40 solder.

Solder Eutectic Alloy At Joanna Izzo Blog
Pros and Cons
4. Weighing the Options
Alright, let's break it down into a clear and concise comparison. Here's a quick rundown of the pros and cons of each type of solder:
63/37 Solder
- Pros:
- Eutectic alloy with a sharp melting point, reducing the risk of cold solder joints.
- Easier to work with, especially for beginners.
- Provides more consistent and reliable soldering results.
- Cons:
- Generally more expensive than 60/40 solder.
- May not be as readily available in some areas.
60/40 Solder
- Pros:
- Typically less expensive than 63/37 solder.
- More forgiving when soldering components with different thermal masses.
- Widely available.
- Cons:
- Non-eutectic alloy with a pasty phase, increasing the risk of cold solder joints.
- Requires more careful technique to avoid movement during cooling.
Ultimately, the best solder for you will depend on your specific needs and preferences. If you're a beginner or working on critical applications where reliability is paramount, 63/37 solder is generally the better choice. However, if you're on a budget or working on less demanding projects, 60/40 solder can still get the job done effectively.
Just remember to practice proper soldering techniques, regardless of which type of solder you choose. This includes using a clean soldering iron tip, applying flux to the joint, and keeping the joint still during cooling. With a little bit of care and attention, you can achieve solid and reliable solder joints every time. Happy soldering!

Choosing the Right Solder for Your Project
5. Factors to Consider
So, how do you make the final decision? Here are a few key factors to consider when choosing between 60/40 and 63/37 solder:
Project Type: Are you working on a hobby project, or a critical electronic device? For sensitive electronics or projects where reliability is crucial, 63/37 is often the preferred choice. For less critical applications, 60/40 can be perfectly adequate.
Skill Level: If you're new to soldering, 63/37's sharp melting point can make the learning process easier and more forgiving. The distinct transition from solid to liquid helps prevent cold solder joints, a common mistake among beginners.
Budget: 60/40 solder is generally more affordable. If you're on a tight budget, this can be a significant factor. However, keep in mind that the cost of potential rework due to faulty solder joints could outweigh the initial savings.
Availability: Depending on where you live, one type of solder might be more readily available than the other. Check your local electronics stores or online retailers to see what's in stock.Ultimately, the best way to determine which solder is right for you is to experiment and see what works best for your soldering style and the types of projects you typically work on. Don't be afraid to try both and see which one you prefer. After all, soldering is a skill that improves with practice, and there's no substitute for hands-on experience.
